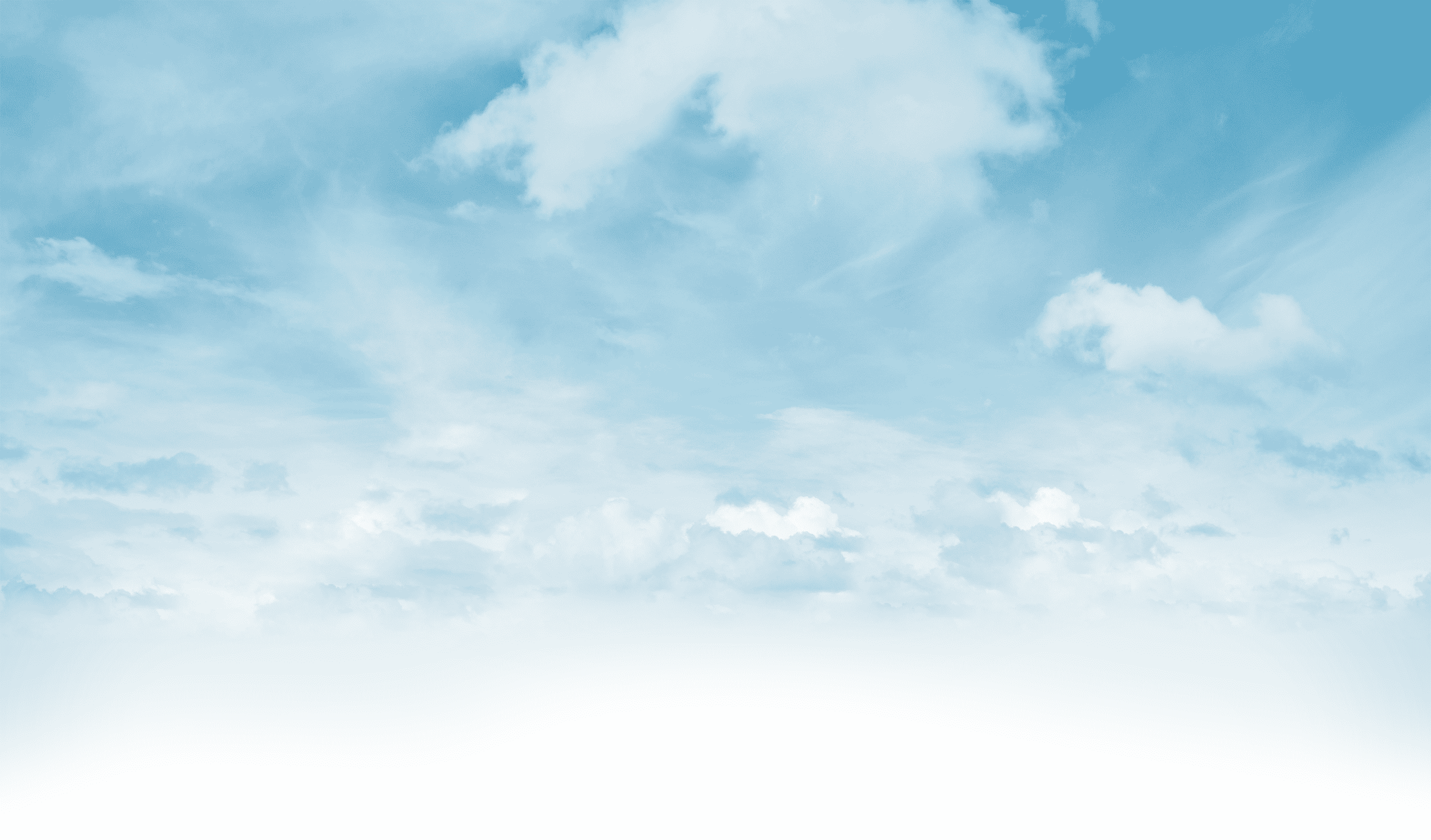
Saving (s)oil, sustainably.
As excavators tirelessly perform their demanding tasks on construction sites with utmost precision, the hydraulic lines of their attachments face various unforeseen challenges. Hose ruptures leading to uncontrolled oil leaks are an unfortunate inevitability, and the consequences are dire.
It's time for the innovative soilution: OILFIX.
Protecting the environment
Reducing costs and downtime
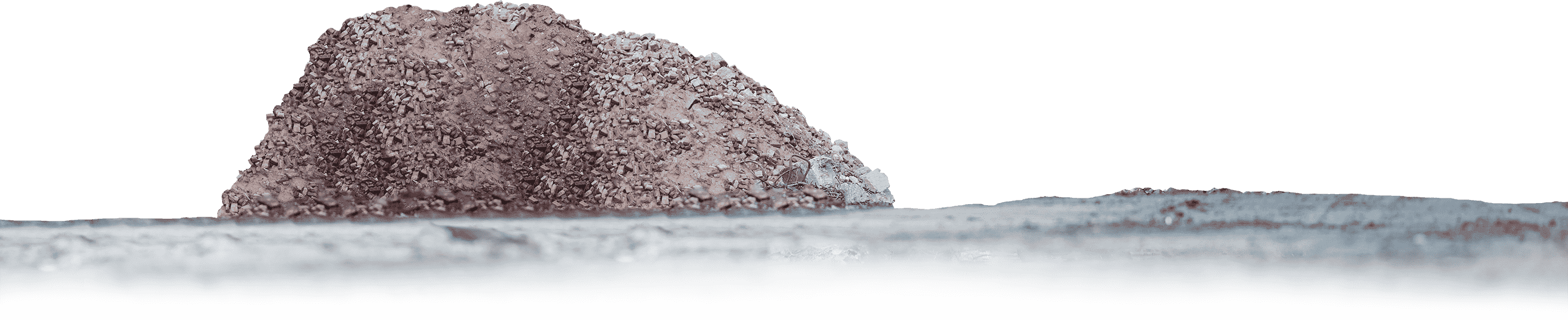
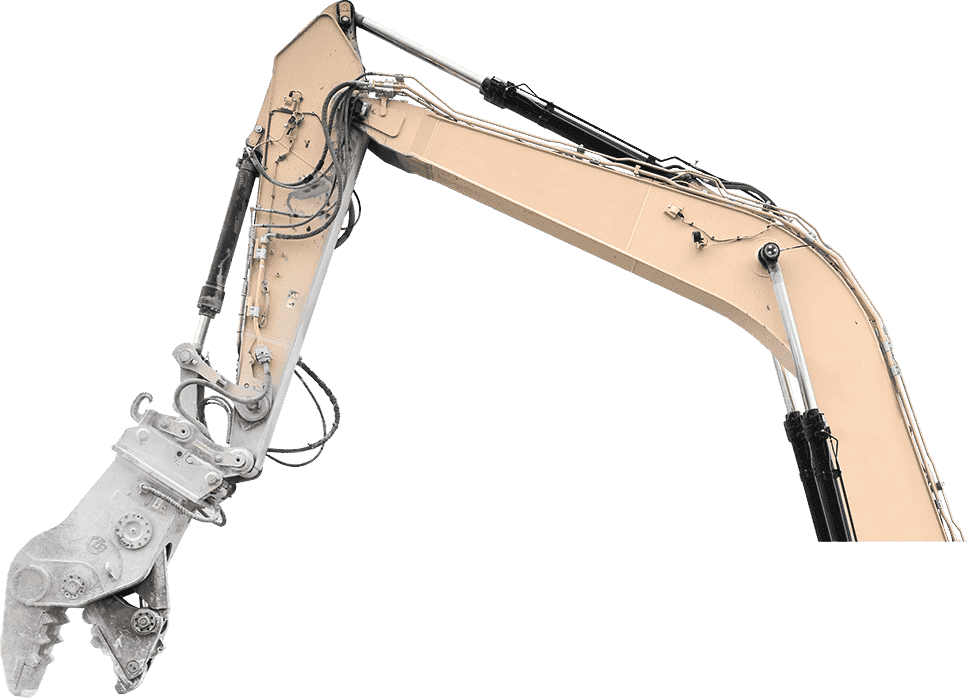
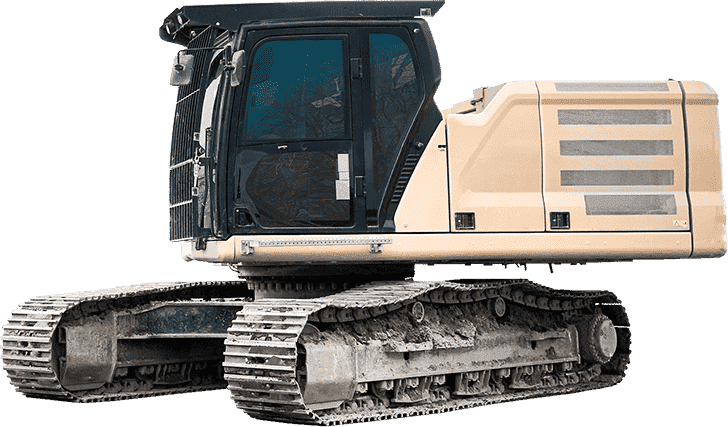
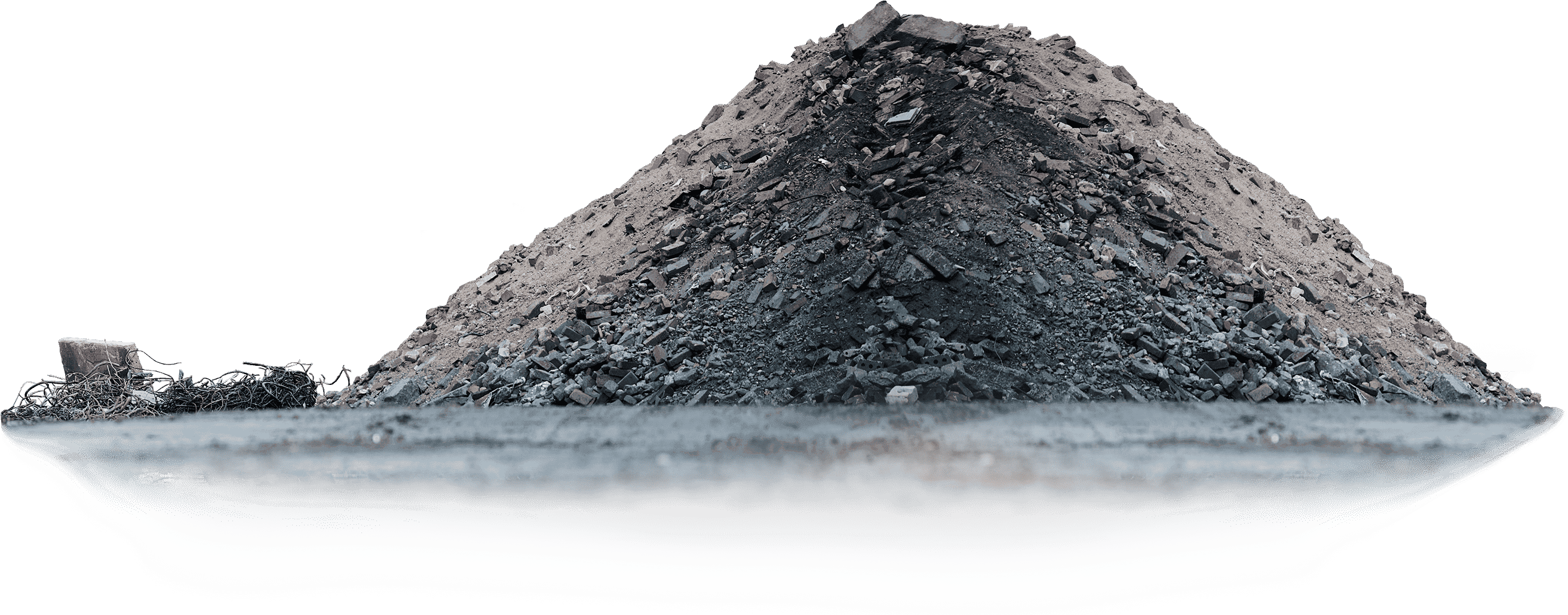
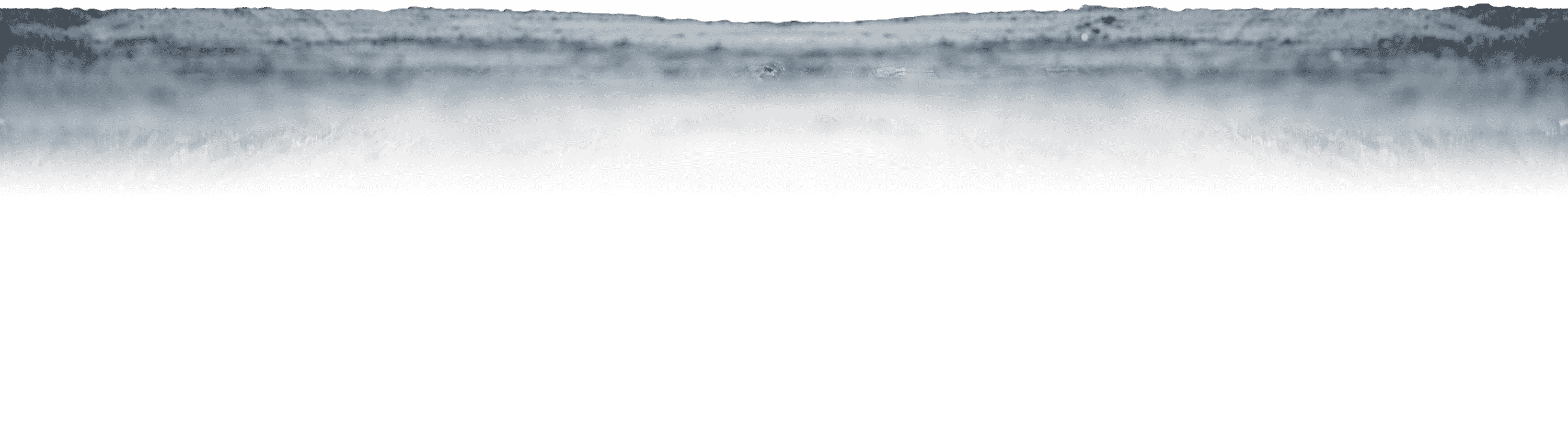
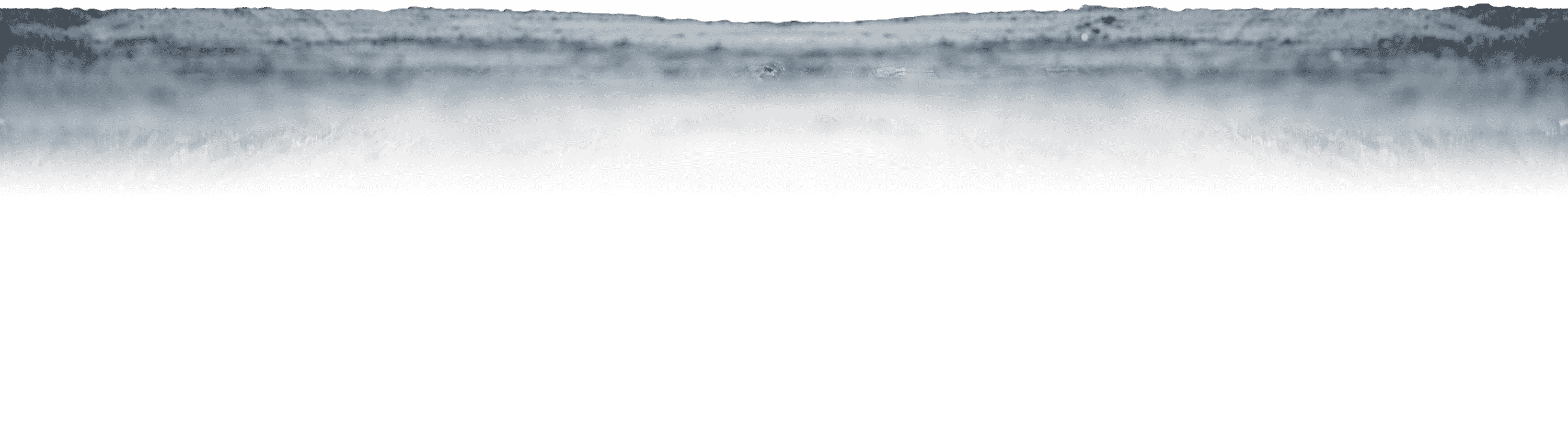
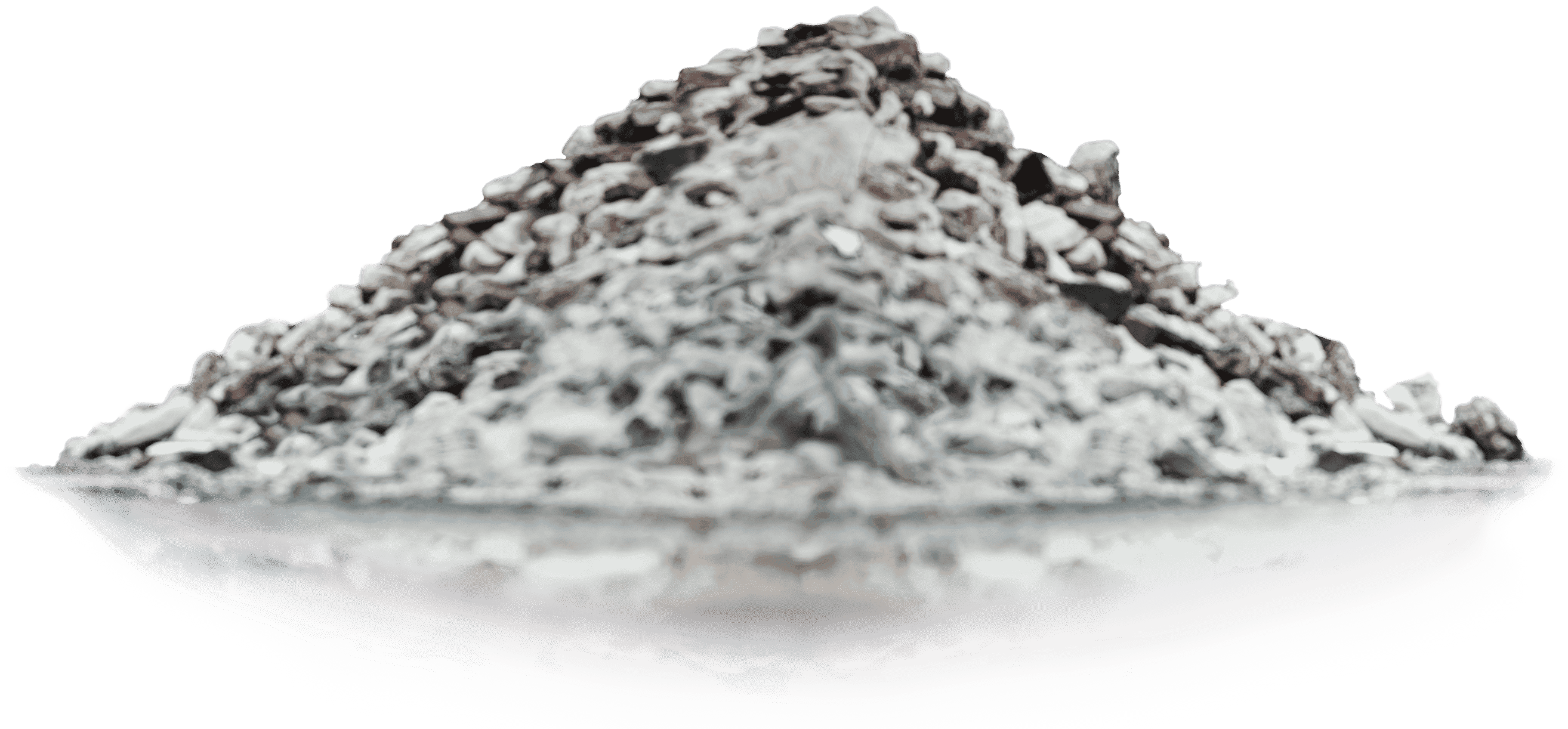
Aging, weather conditions, and unforeseeable external impacts expose hydraulic hoses of attached equipment to substantial threats.
The outcome? Unpredictable ruptures causing uncontrolled oil leaks.
With every additional second, hydraulic oil relentlessly streams from the ruptured hose and typically seeps into the soil.
Until now, addressing these leaks required lowering the excavator boom and shutting down the machine, a process that could take up to thirty seconds, depending on the excavator's size.
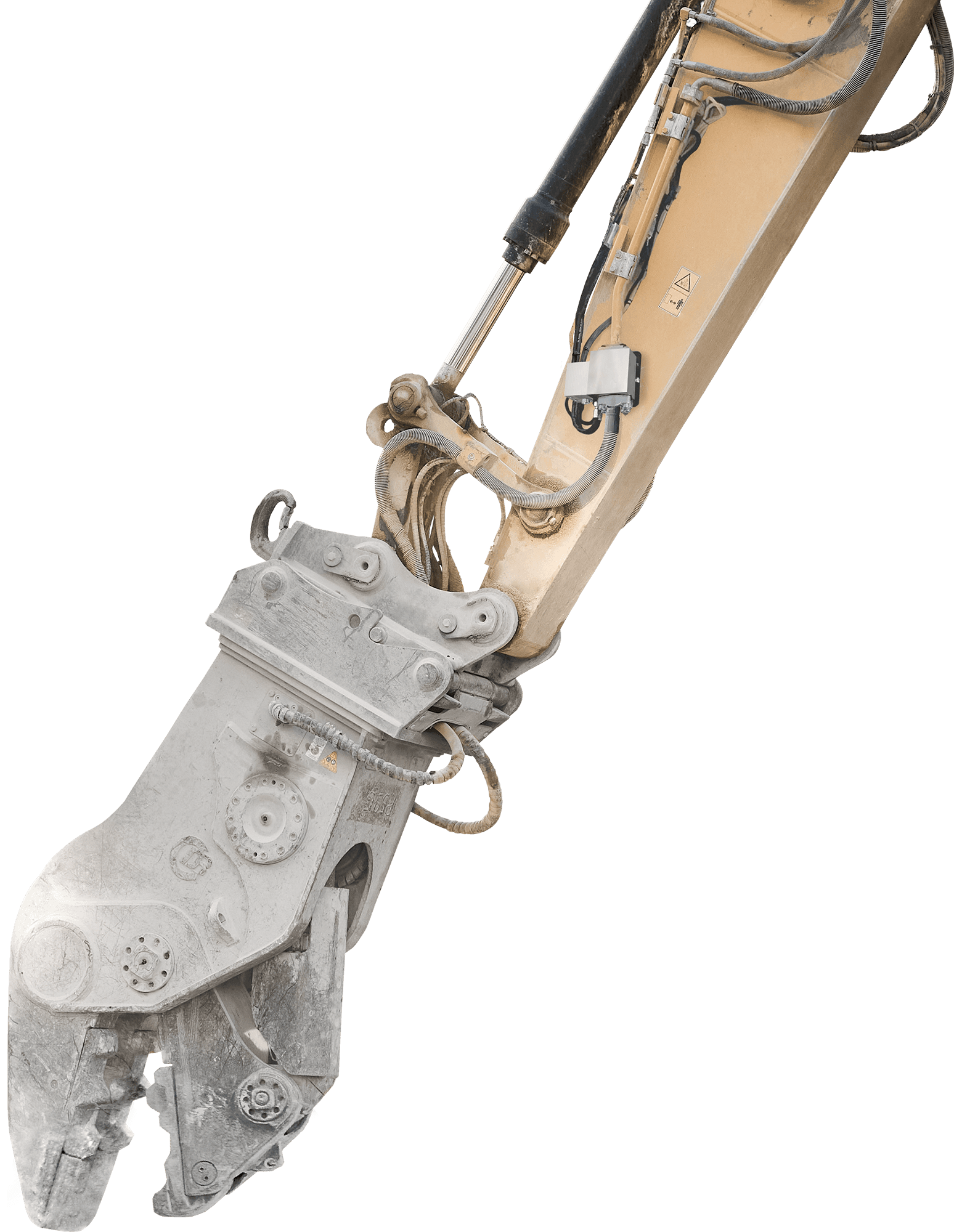
The so(i)lution: OILFIX
The OILFIX valve blocks are mounted on both sides of the excavator boom, transforming the previously existing mechanical shut-off valve into a remote-controlled innovation: By pressing the OILFIX button in the operator's cab, the machine operator can intervene directly in the event of a leakage and stop the oil flow instantly.
OILFIX radically minimizes oil pollution. And despite the burst hose, the excavator remains fully functional and can easily be moved into a repair position without further leakage.
stopping spills, sustainably
We're looking forward to hearing from you!
The origin of OILFIX? Construction sites.
Berthold Winz, who came up with the idea of OILFIX, has spent over three decades working with construction and agricultural machinery, specializing in delicate demolitions and complex inner-city deconstruction projects. As a passionate machinist and successful entrepreneur, he has witnessed numerous costly oil leakages firsthand. Unwilling to accept the environmental pollution, financial burdens, and safety risks caused by hose bursts, Berthold, a trained machinery mechanic, took matters into his own hands and developed the so(i)lution: OILFIX.
/)
Berthold Winz joined forces with Christoph Sauer to combine his practical construction site experience with commercial acumen. The tech-savvy logistics specialist Sauer quickly became enthusiastic about the innovative idea and took over the further development of the product to market maturity. The two managing directors established OILFIX GmbH in 2023 to make construction work more environmentally friendly and economically viable. With a skilled team, OILFIX offers a viable answer to the age-old problem of hose bursts.
/)
key questions answered
What is a hose burst? What happens if a hose bursts?
Hydraulic systems turn various machines into valuable commercial vehicles for construction, agriculture, forestry, or transport. For power transmission into motion, the required hydraulic oil is pumped through dedicated lines, either pipes or hoses. Hydraulic hoses in moving parts of machines age naturally due to sunlight, dirt, or material fatigue. The DGUV (German Statutory Accident Insurance) recommends maintenance intervals to prevent hose bursts during ordinary operations. However, most hose bursts in practice are caused by external influences; for example, when a demolition excavator gets caught on a piece of steel and individual hoses are torn off. Uncontrolled oil leaks from defective or torn pipes can lead to environmental damage, consequential costs, and increased health risks. OILFIX can significantly reduce oil leakage in the event of a hose burst. The operator can move the excavator to a suitable location without further oil leaking, limiting contamination and speeding up clean-up operations. The innovation minimizes downtime and significantly reduces the negative impact on the construction site's processes and performance.
How exactly does OILFIX work?
OILFIX valve blocks are mounted on both sides of the excavator boom in replacement of the ball valves and connects to a switch in the driver's cab via an electrical cable. In the event of a leak, the machine operator can immediately stop the oil leakage by pressing the OILFIX switch. This swift response allows for a rapid containment of the oil leak, minimizing damage. Despite the lines being shut off, the excavator remains functional so that the machine can continue to be operated and moved to a repairable state without any further oil leaks. After the damaged hydraulic hose is repaired or replaced, the hydraulic oil circuit can be reactivated at the push of a button. OILFIX is ready to prevent future leaks whenever a hose bursts again.
What is the difference between OILFIX and a line rupture protection valve?
Current pipe rupture devices serve as essential safety valves for load holding, preventing uncontrolled lowering of the boom in case of a pipe rupture on the excavator. While effective in safeguarding against injuries to site personnel, these devices do not halt uncontrolled oil leakage. During a pipe break, a fixated excavator arm can still lead to potential ecological and economic damage within seconds. OILFIX addresses this limitation as a crucial enhancement to existing excavator safety mechanisms and enables immediate spill containment.
How often can I use OILFIX?
Despite preventive measures and careful working methods, hose bursts remain commonplace on construction sites. OILFIX is designed to significantly mitigate the consequences of a hose burst and ensure a swift return on investment. With a one-time installation, OILFIX reduces damages time and time again: By pressing the switch in the driver's cab, the operating voltage is immediately shut off, and the OILFIX valves close on both sides. After the damaged hose is repaired or replaced, the lines can be re-opened by simply pressing the OILFIX switch again, fully restoring the hydraulic oil circuit. With the one-time installation of OILFIX, both the excavator and its operators are always prepared for the next potential hose burst.
Intrigued to learn more?
Let‘s talk about saving (s)oil. We look forward to hearing from you!